There’s no escaping the fact that resin bound gravel installation is a seasonal job. With polyurethane binders being sensitive to temperature and moisture, it’s almost inevitable that in the UK from around the end of September, the number of good days to lay resin bound drops dramatically.
Resin bound gravel binders are generally formulated with curing times based at temperatures at a very mild 20°C and usually give an installer between 30-60 minutes to spread and trowel the surface before becoming tacky and unworkable. When air temperatures fall below 20°C the curing time of the resin component starts to lengthen
Resin bound catalyst: reduces curing times
If the ground and air temperatures are too cold, the reaction of the part-A and part-B of the resin slows down and the lower the temperature, the slower that curing process is. When the surface curing process is too low, this can leave the resin binder vulnerable to dew, condensation or rain collecting on the top. Those who have worked with resin for a while or have attended any resin bound training courses will know that if there’s one thing you need to avoid, it’s moisture.
We know that we can’t do anything to make the weather any warmer, so we have to adjust the mix to help speed up the curing times. Adding more gravel, sand or resin doesn’t help to make a positive impact on this curing time, so a resin bound catalyst (also called accelerator) can be added to help speed things up.
In reality, you’re not actually making anything cure any quicker than it would normally, you’re just adding a chemical to counteract the slow curing time to make the mix go off in the usual timescale which will help to avoid long or overnight curing of the surface.
How much catalyst should you use?
This can be difficult to pinpoint and will vary from manufacturer to manufacturer and even between resin formulations (like UV versus Non-UV) and our best recommendation is to check with your supplier or manufacturer.
It’s also wise to stick with the same manufacturer for both your resin binder and your accelerator, as the products you buy are most likely to be designed to work with each other and crossover between manufacturers may cause adverse effects. So for example if you buy PermaBound resin, you should buy PermaBound catalyst.
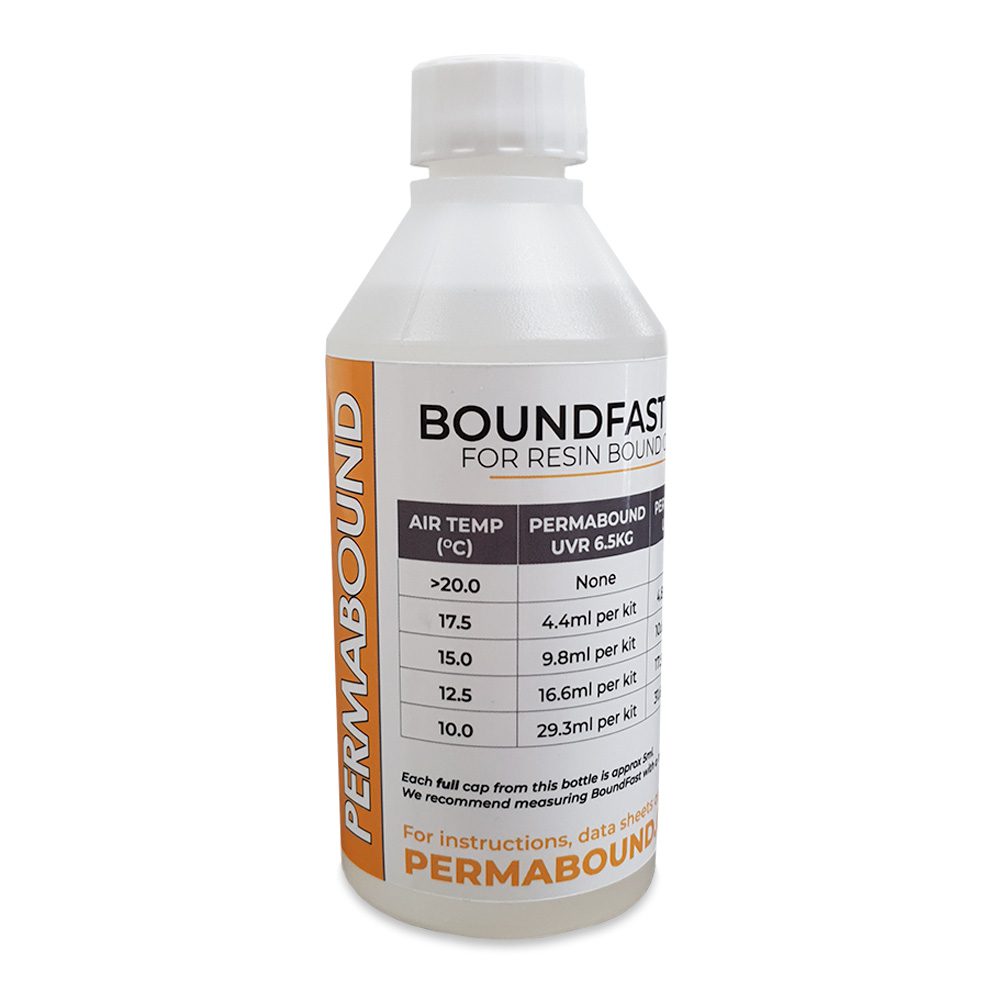
If you are using our PermaBound UVR resin, you can see the table below which gives an indication of how much catalyst should be used to make sure the resin cures in the usual timeframe. If you’re using a different product, you should speak to your supplier or the manufacturer to get guidance on how much to add for your specific materials.
Air Temp (°C) | PermaBound UVR 6.5kg | PermaBound UVR 7kg | PermaBound UVR+ 7.5kg |
---|---|---|---|
>20.0°C | None | None | None |
17.5°C | 4.4ml per kit | 4.8ml per kit | 5.1ml per kit |
15.0°C | 9.8ml per kit | 10.6ml per kit | 11.3ml per kit |
12.5°C | 16.6ml per kit | 17.9ml per kit | 19.2ml per kit |
10.0°C | 29.3ml per kit | 31.6ml per kit | 33.8ml per kit |
How do I mix catalyst with resin?
The BoundFast catalyst is supplied in a 200ml bottle which comes with a 5ml cap. This cap can be used to make approximate measurements, but we would always recommend using a 1ml syringe to add any catalyst to resin.
A 1ml syringe gives you a large amount of control over exactly how much catalyst is added to the mix and while may take a little more time than approximate ‘capful’ measurement, it will all but guarantee the consistency of your curing times.
Ensuring the syringe is clean and dry, draw up 1ml at a time and slowly inject the catalyst into the Part A component of your resin binder. Repeat the process until you’ve reached the required dosage appropriate to the temperature table above.
You can then mix the two resin components together (parts A & B) according to the manufacturer instructions.